It goes without saying that concrete is big business. It is one of the oldest building materials known to man with a rich history that stretches back, astonishingly, over 9000 years. It is therefore remarkable that the product itself has remained relatively unchanged throughout this time and is still the most used building material by a considerable distance. In fact, behind water, it is the second most consumed material in the world. Unfortunately, the world has changed in the intervening millennia. While most of these changes are positive, it is no surprise that some things have deteriorated. Now, more so than ever before, a closer eye is needed on the environmental impacts of our every move and concrete, like anything else, is coming under scrutiny. Concrete, while being of huge importance to the building and construction world, comes at a heavy environmental price. The emissions generated from its production are enormous and it is important to offset this in some way. To this end, innovative minds have been working overtime to ensure that concrete has a sustainable future within the industry with carbon extraction gathering traction on jobsites and projects around the world.
Extraction is not the only answer, however. In order to work towards a more environmentally positive path, other solutions are also required which can work alongside this to reduce the impact of concrete. While much is currently being done to counteract the environmental effects of construction, challenges remain. Throughout the industry, stakeholders are working tirelessly to develop new and innovative methods of ensuring the work we do is cleaner, more sustainable and has a lower environmental impact. Despite this, the unfortunate truth is that concrete is still one of the worst offenders when it comes to carbon emissions. However, scientific breakthroughs are offering a glimpse into the future. While this is clearly something to be welcomed, it is not a magic bullet that will allow the industry to sleepwalk into environmental disaster.
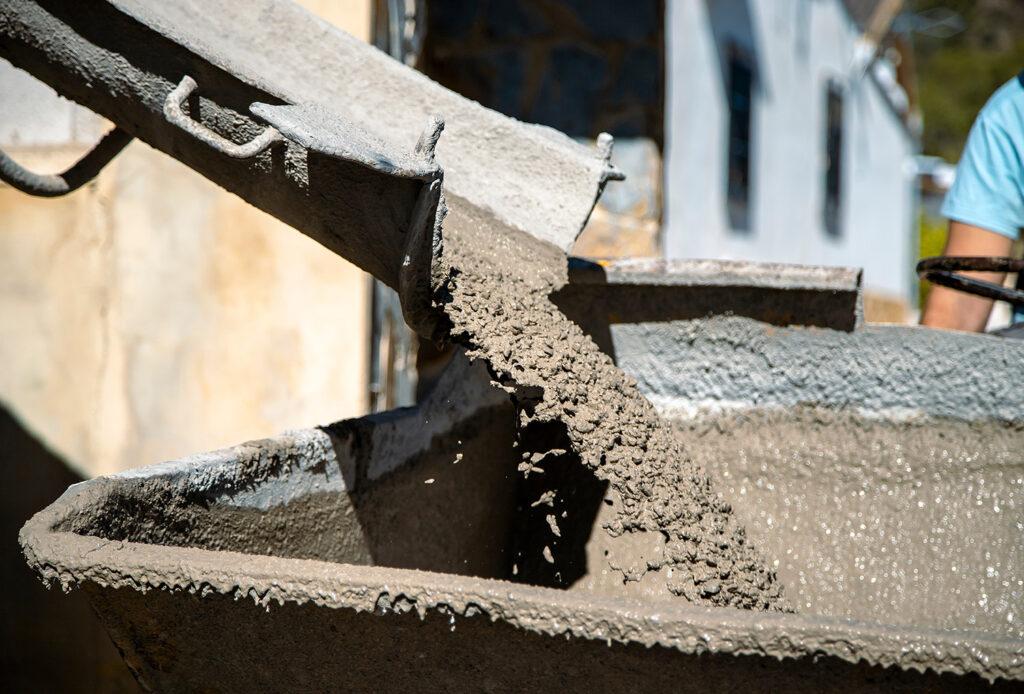
The reason that carbon extraction is not a catch-all solution is a historical one. Extraction only works for new concrete and simply put, there is an enormous amount of concrete already out there in the world. These buildings and the concrete they are made from are at various stages of disrepair and reliability. It is reported that fissure repairs because of cracks costs the U.S. industry $12 billion every year. This figure, coupled with the environmental cost of these repairs, mean that the concrete issue is not one that can be solved easily. Thankfully, there is hope. Research emerging from the U.K. suggests that by adding an enzyme found in red blood cells called Carbonic Anhydrase, concrete can “self-heal.” If this proves to be financially sustainable, it could result in massive savings, on various levels, across the industry. This incredible scientific breakthrough works by adding the enzyme to concrete powder. The resulting reaction helps the material turn CO2 from the atmosphere into calcium carbonate crystals which restores cracks in the material.
Resilient Materials 4 Life (RM4L) is a U.K. based program funded by the Engineering and Physical Sciences Research Council (EPSRC). The purpose of the program is “to transform the Nation’s built environment through the provision of a sustainable and resilient infrastructure, using low carbon, adaptable and sustainable construction materials.” To do this, RM4L is using a combined approach, weaving science and engineering together through both fundamental and application-based research. Like the situation in North America, the program is looking to initiate change due to an ever-growing need. As we see infrastructure networks crumbling and the enormous amount of money required to repair them, the focus is shifting towards a more preventative and sustainable approach. “Activities ranging from experimental research to modelling and simulation will enable building materials to be designed and manufactured that can adapt to their environment and ensure long-term reliability over the life-cycle of the structure that they comprise.”
“From the creation of microcapsules which contain healing agents to bacterial healing techniques, it is safe to say that a huge amount of research and testing is going into this process.”
While there are many ways of producing such a scientific reaction, each are based on different scientific methods. From the creation of microcapsules which contain healing agents to bacterial healing techniques, it is safe to say that a huge amount of research and testing is going into this process. Each method is considered to have its own strength within specific contexts and many of them are genuinely considered to have huge potential in becoming a standard feature in the market. Currently, Europe is leading the way in terms of usage. However, the global outlook, and North America in particular, makes for exciting viewing. In fact, even the most conservative of predictions is impressive. Research conducted by Market Research Future predicted that the global self-healing concrete market will expand by an incredible 24% annually. Even more impressive is a study produced by Grand View Research which claims that the U.S. market for self-healing concrete is anticipated to expand at a CAGR of 34.9% in terms of revenue by 2027. According to the report, “The rise in demand for eco-friendly and sustainable constructions with high endurance is expected to drive the demand for self-healing concrete. However, nowadays, the proportion of non-hardening cement in the construction process is less, along with growing trends of fast construction. Moreover, unskilled labor is scaling the proportion of natural cracks in walls and columns of buildings.”
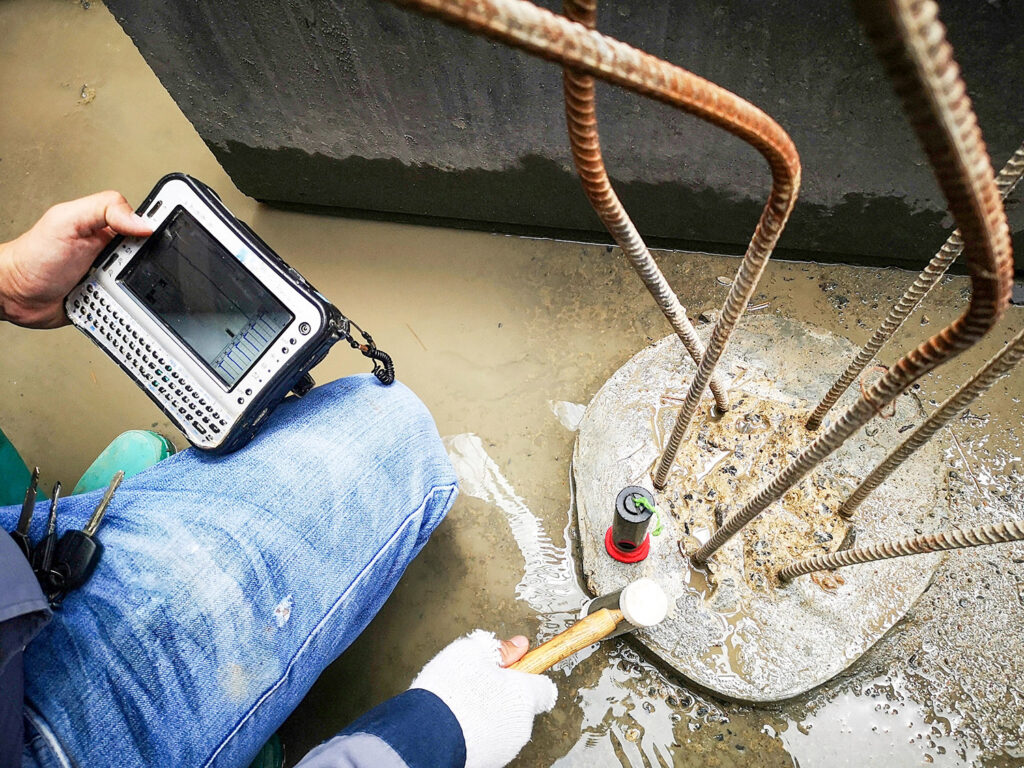
While it is generally accepted that concrete is the go-to for most building work, it is not without its drawbacks. As the recent Infrastructure Bill shows, vast sums of money need to be made available to repair and reconstruct failing structures. So, is this the answer? According to Basilisk Concrete, the benefits are manifold. They claim that by sealing cracks, self-healing concrete ensures the material is waterproof. In addition to this, it states that the product ensures reinforcement savings of over 40% and, by reducing the need for repairs, it has a 50% reduction in the CO2 footprint that regular concrete has. Those at Basilisk Concrete believe that, despite the product being in relative infancy, it holds huge advantages over regular concrete. “One of the properties of concrete is that it will always crack. With a good design and good application this cracking can be reduced, but even the little (hair) cracks can cause big problems. Cracked concrete has pore water resistance and the freeze-thaw resistance of the concrete will be limited. Also, the durability of cracked concrete will be greatly reduced. Through the cracks moisture and oxygen is able to reach the steel reinforcement which can cause the steel to corrode. This could cause serious damage to the concrete structure.”
Self-healing concrete has not yet taken over the industry. That much is true. There are still issues with initial pricing and, more pressingly, its benefits are not yet widely known. However, the potential to be a real game changer is undoubtedly there. Further work may be needed to prove to the industry that it can offer a genuine alternative to standard concrete. Only time will tell if this can happen. What is clear though, is that if self-healing concrete proves to be a workable solution, we could see a massive reduction in material costs, labor hours and, most importantly, carbon emissions.