Sustainability needs to be more than just a vague goal for a company – it has to become part of its ethos. It is easy enough to spout marketing jargon and gesture in the direction of environmental concerns. The Industrial Revolution made possible every astounding technological innovation that we, as humans, currently enjoy. From transportation and infrastructure, to communications and medicine, all of it has been forged in the fires of modern manufacturing. These miracles of the modern age have come with a cost, of course. We have a changing environment to come to terms with and business everywhere must now acknowledge that new ways ahead are needed. And equally, to recognize that with responsible innovation comes economic benefit. In the water management industry, multinational outfit Forterra Pipe & Precast sees both its products and processes in alignment with those concerns.
It starts with the implementation of low-carbon cement, which is used across its range of products within Canada. Beyond reducing its carbon footprint through better materials, there are the protections the products offer from the often-devastating effects of climate change. Forterra’s stormwater management range is industry-leading and helps citizens enjoy high-quality water without the pollutants carried by ever-increasing storm-surges. VP of Business Development, Leo Steffler said, “We are the market leader in the province (Ontario) in stormwater quality products. Our history with that goes back to 1995. Since we were the first ones in it, we have licensed technology. Our product lines of Stormceptor, Jellyfish, and Filterra, they’re brand names. We have a good following and we are developing more products internally for stormwater storage and quality, so I think that’s been a big strength. But it’s something good for the environment, and clean water is important for everybody.” It is here that Forterra’s X-Stream retention system is worth particular note. Installation of pre-cast boxes is quick and they can be arranged in a variety of ways to suit the context. Importantly, unlike other systems consisting of less-rigid materials, the X-Stream is built to withstand all kinds of traffic loads. As Steffler described it, “You don’t have to worry about driving a tractor trailer over it, and it’s also long-term. Our products have a proven history of a 100-year lifespan.” Building products that last is fundamental to both combatting climate change and also ensuring customer satisfaction as well. Business and sustainability do, in fact, go hand-in-hand.
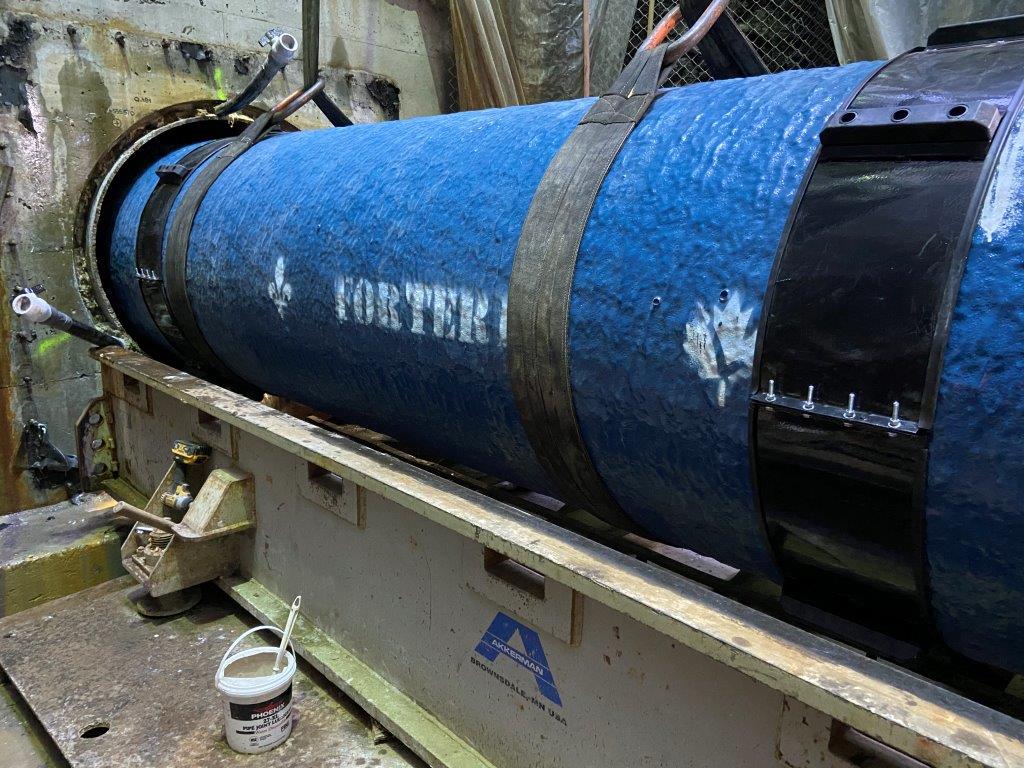
Forterra sees another synergistic opportunity developing with its new wet-cast facility that is soon to begin construction. It’s an opportunity to grow as a company and also a massive benefit to both the customer and the environment alike. Steffler said, “We see an opportunity for us to displace cast-in-place structures. We need to grow the business organically. So, we’re going to expand that product line. The advantage of precast is it basically it saves society a lot of time. Take a culvert crossing, for example; it’s constructed on-site with ready mix, with less quality, probably could take months. We can do a crossing in a day with pre-cast, so there’s a big benefit to the owners, the specifiers. And you also get a higher-quality product because it’s made in a controlled environment.” Win-win scenarios like this also demonstrate how thinking in terms of environmental sustainability often ends up in significant savings via greater efficiency. Everyone benefits.
In support of efforts to have its projects reduce their footprints, Forterra has moved firmly into micro tunneling. In contrast with the large excavation required for bigger piping, micro tunneling merely requires a small hole drilled down through the ground that piping can then be dropped into and pushed through the shaft. It is a significant reduction in disruption to the surrounding area. As Steffler said, “I think that product line is going to continue to grow because again, if you don’t have to disturb society, if you can keep traffic moving, you know it’s really a benefit.” Along the same lines, there’s currently an industry-wide difficulty with excess soils from excavations that needs to be moved off site. Flexible pipe products need select granular material compacted all around the pipe. Whereas Forterra’s rigid piping can use the native backfill to cover up after construction. Steffler explained, “Our product is very rigid and if we have a good bedding up to spring line we can use the native back backfill, so that’s a big benefit to the contractor and to the environment as well. You’re saving that gravel. That stone, eventually you’ll run out of it. So, if you can leave that native material on site, that’s a great thing. And our product fits well with that.”
“Forterra’s rigid piping can use the native backfill to cover up after construction.”
Parallel to those efforts, the company also aims to lower its impact through structural means such as installing more efficient lighting in its offices. Similarly, each time Forterra upgrades its plants, more efficient motors are put in place to continually improve its relationship to the planet. It is an on-going process, but the company sees itself at the forefront of the construction industry’s efforts to act responsibly.
The pervasive challenge of the last 15 months has, of course, been the Covid pandemic. With both business and personal livelihoods at the mercy of the virus, navigating a company through the storm is an ongoing effort. It has been a challenge, however, that Forterra has managed to meet well. Balancing a very busy year with the necessities of extremely heightened health and safety requirements required buy-in across the board. VP & General Manager Shane Egan said, “The employees have done a tremendous job in the plants, and I would say we’ve got over 50% of our office staff working from home. They’ve done a tremendous job. I don’t think we’ve missed a beat during a particularly busy time. So, we’ve done really well. We’ve had, zero cases in Canada. We’ve implemented restrictions well. The team members have managed this situation extremely well.” Covid has laid the groundwork for secondary challenges as well. Supply-chains have been interrupted on a global scale. The costs of materials has drastically increased in many cases, and in others materials are difficult to source at all. As Egan noted, “The supply of the raw materials particularly, steel and resin, rubber-based products will require continued flexibility and nous to steer through the choppy waters of this global scourge.”
“We deliver what we say we’re going to deliver. We don’t like to let anybody down.”
It’s not only Forterra’s products that last. Integrity has multiple meanings for the company. The products are designed to continue to work for a very long time, yes. But so are its relationships. In a highly competitive market, companies that don’t back up their word aren’t long for the world. Steffler explained, “I think what we’ve never done is over-committed, or oversold. We deliver what we say we’re going to deliver. We don’t like to let anybody down. I think that’s really been a feather in our cap.” Bolstering this notion, Egan added, “Well, I think it ties in with that word integrity, right? It ties in with one of our values. It’s one of our six core values; that word integrity.” Things that are built to last the test of time aren’t cheap, quick, or easy. Durability requires real commitment to excellence. Steffler summed it up with an apt aphorism, “If you want to last in this industry, you have to wear well.”
Lasting words, indeed.